Lean Manufacturing: The Path to Operational Efficiency
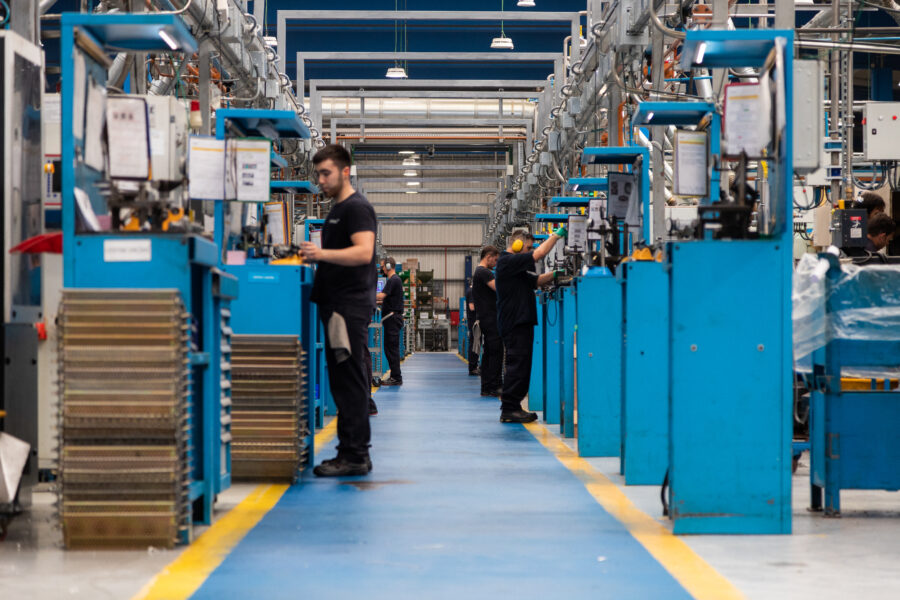
In an increasingly competitive and dynamic environment, operational efficiency is a key factor for the success of any organization. One methodology that has proven to be highly effective in improving productivity is Lean Manufacturing, a system and industrial management approach aimed at minimizing waste and maximizing added value throughout the production process.
The term Lean Manufacturing, or Lean Production, first appeared in the 1970s in the book The Machine That Changed the World by authors Womack, Jones, and Ross, and is based on the Toyota Production System (TPS). This system, developed by the Japanese automotive company Toyota, was designed to optimize its production chain by eliminating activities that do not add direct value to the final product, such as waiting times, excess inventory, unnecessary transportation, among others. Over time, this methodology has been adopted by numerous industries worldwide due to its ability to improve not only efficiency but also the quality and flexibility of production processes.
The Pillars of Lean Manufacturing
The core of Lean is based on continuous improvement (Kaizen) and the identification of activities that do not generate value, known as “waste” or muda in Japanese. The goal is to eliminate or minimize them, thereby increasing the performance of the production system. There are seven key types of waste that Lean Manufacturing seeks to eliminate:
- Overproduction: Producing more than necessary or before it is required.
- Inventory: Accumulating raw materials, work-in-progress, or finished goods in excess.
- Unnecessary Movements: Personnel movements that do not add value.
- Transportation: Unnecessary movement of materials between different areas.
- Waiting: Downtime between process stages.
- Defects: Products or services that do not meet quality standards.
- Overprocessing: Doing more work than necessary or using inappropriate tools.
In addition to focusing on waste reduction, Lean relies on other fundamental principles, such as work standardization, customer focus, and employee involvement in the search for improvement solutions.
To achieve these objectives, Lean Manufacturing uses a series of tools and concepts, including:
- VSM (Value Stream Mapping): A detailed analysis of the value stream that helps identify areas for improvement across the supply chain.
- 5S: A methodology focused on creating and maintaining an orderly and efficient work environment.
- Kanban: A system that regulates production flow using visual signals, reducing overproduction.
- Andon: A visual tool that alerts operators and supervisors to issues on the production line.
- SMED (Single Minute Exchange of Die): A technique for reducing setup and changeover times between operations.
Teknia and Its Commitment to Lean Manufacturing: A Local Approach for Global Impact
At Teknia, the implementation of Lean Manufacturing is not just a methodology but an integral part of its operational excellence model. This global initiative aims to transform all plants to achieve the highest levels of efficiency and quality. The commitment is clear: reduce waste, improve, and optimize production processes. The Lean project at Teknia addresses both customer demands and the strategic objectives of enhancing economic and operational performance.
One of the keys to success is local implementation in each plant. Each facility will have an Operational Excellence Leader responsible for directing the Lean evaluation and developing a personalized work plan aligned with the specific needs and characteristics of each plant. This approach ensures that the methodology effectively adapts to each operation, supported by global and regional oversight.
Interested in our Press Kit?